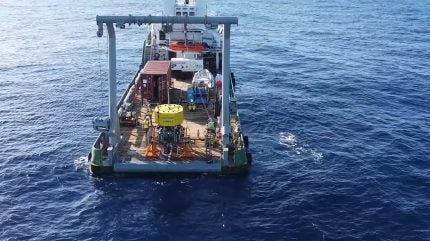
Impossible Metals, a company is building underwater robotic vehicles to collect critical metals from the seabed, last week (13 May) announced that it had successfully tested its Eureka II autonomous underwater vehicle (AUV) in deep water.
It said the test, carried out in April, was the first deep-water dive by an autonomous vehicle designed specifically for deep-sea mineral harvesting – and it takes the firm closer to its goal of “responsible seabed mining”.
Oliver Gunasekara, co-founder and CEO of the company, said of the test: “After successful autonomous collection of rocks late last year, we have now proven autonomous navigation capability of Eureka II in the deep ocean off Florida. We plan to test Eureka III, our production-sized system, next year.”
Part of the Impossible Metals spiel is that the “selective harvesting” of which its robots are capable minimises any environmental impact. Environmental activism group Greenpeace, among others, has argued that deep-sea mining would be an “environmental disaster”, even name-checking Impossible Metals in a recent article that decried “plans to exploit the depths of the Pacific Ocean and the Arctic”.
To understand more about Impossible Metals’ AUVs, deep-sea mining plans and environmental outlook, Mining Technology spoke to the company’s co-founder, chief operating officer and chief technology officer Jason Gillham.
Stu Robarts (SR): Why was Impossible Metals founded, and what is its story so far?
Jason Gillham (JG): There’s a massive issue with global warming and, ultimately, to solve that, there’s a massive need for critical minerals as we work to decarbonise the energy system, move away from fossil fuels and get towards stabilising temperatures on the planet.
Access the most comprehensive Company Profiles on the market, powered by GlobalData. Save hours of research. Gain competitive edge.
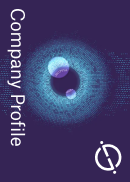
Your download email will arrive shortly
We are confident about the unique quality of our Company Profiles. However, we want you to make the most beneficial decision for your business, so we offer a free sample that you can download by submitting the below form
By GlobalData
In order to have those levels of metals, the current ways of terrestrial mining have their downsides, and so there’s interest in exploring deep-sea mining as an alternative way to do that. We looked at the prevailing ways that industry is looking to do that now, and we felt that we could do it in a better way.
SR: Just how important are critical metals and how scarce do they risk becoming?
JG: The demand for critical metals is increasing at a growing rate, driven by increased consumer electronics and driven by electric vehicles, substantially. The need for these metals continues to grow.
Today, these metals are predominantly collected from terrestrial mines in rainforests in Indonesia, mined with child labour in a number of cases. We’re able to not have a number of those negative impacts with a deep-sea mining approach.
SR: Why is it important to explore seabed mining as an alternative to land-based mining?
JG: Today, the grades of metals on these terrestrial mines are decreasing. As a result, there are substantial environmental impacts when we are collecting metals from terrestrial sources.
Additionally, as we have decreasing grades of metals on terrestrial sources, the pricing for these metals is going to have a big impact, and that will really hinder adoption of some of the green technologies that we need to ultimately decarbonise.
Seabed mining becomes a solution and a source of these metals that certainly will help to alleviate some of those environmental issues with terrestrial mining, as well as improve pricing and adoption of the technology as the demand for the metals grows substantially.
SR: What concerns do people raise about seabed mining and does Impossible Metals address them?
JG: The prevailing concerns, as I understand them, related to deep sea mining, come from a number of environmental impacts, one of which is sediment plumes – and we’ll talk a bit about addressing that. Another becomes noise and activity within the water that has an environmental impact. Then, just the nature of if we use a suction-based system or an indiscriminate system for collecting nodules – then the systems can kill life that it’s driving over.
Our collection technology aims to mitigate those downsides by using a fleet of autonomous robots that hover over the surface of the seafloor, don’t actually touch the seafloor with either tracks or the collection system. Using selective harvesting arms, we’re able to leave nodules undisturbed – so we can leave a percentage of nodules undisturbed – we can identify life, leave that life undisturbed.
And then, by staying over the seabed and selectively harvesting, we’re not generating this plume from the collecting system either.
SR: What scope is there for potential unexpected consequences of seabed mining?
JG: I would say that there is not going to be a yes or no answer to that, in the same way that there will never be a yes or no answer to that with any human impact on any project. That makes it a complicated or not-straightforward question.
The work that we will be doing will have an impact. Even with our minimally invasive approach, there is an impact – and it’s critical as a society for us to understand and study those impacts and then collect these metals in a way that has a net benefit for the planet but also has minimum negative impacts.
SR: How does the commercial return of selective seabed mining stack up against dredged seabed mining?
JG: There are two main reasons why the selective harvesting approach has economics that are favourable. The first is the lack of a need for specialised and dedicated mining vessels, the ships that we will be using to transport the ore to the field and back are the same ships that we’re using to service the fleet of robots that are coming to the surface, and so we have substantial capital expenditure efficiencies with our selective harvesting approach because of that.
The other real impact becomes the parallel nature of our fleet. We really don’t have single points of failure, so that becomes another benefit. We may have arms fail, we may have robots fail, but as a continued operation, we don’t have these opportunities for single points of failure in our system.
SR: How were the AUV robots developed, where is Impossible Metals up to with them and what does the future look like for them?
JG: When we started the project, we really stepped back and said: “Fundamentally, what are we trying to solve here? Fundamentally, we need to get rock from the deep ocean to the shore.”
We really stepped back and looked at a full range of options of how to go about doing that, and that’s really what has then led to the architecture that we’ve selected and developed.
We started with an initial proof-of-concept system, this was a lower-cost system, something that was not depth-rated but really proved out the two key enabling technologies within our system, one being the arm and the other being the buoyancy engine. With that proof of concept, we demonstrated it live for a number of people within the industry a year ago, in May last year.
This year, we’ve then progressed with Eureka II, so that’s where we’ve demonstrated deep-water operations of our collection system. We just finished last month our first deep-water dive with that Eureka II system.
Right now, we’re progressing into our Eureka III system. This will be the first commercial-sized AUV that we’re looking to test in the water, giving an opportunity that we may be the first company to have tested their commercial-sized collection equipment.
SR: What were the learnings from the recent Eureka II test that you are taking forward into the third version?
JG: One of the key learnings really had to do with the launch and recovery of the system. This style of vehicle is different to many offshore robotic systems in that we don’t have the ability to just land on our legs in the same way that other robotic systems can just land on the deck.
Our launch and recovery system certainly needed iteration through our offshore testing in order to ensure that we were able to handle the sea states that we were facing. That was one of the learnings.
Then, the second, during a lot of our testing, we maintained a tether on the autonomous vehicle, and, unfortunately, that broke at one point. Fortunately, being an autonomous vehicle, it was able to come up to the surface on its own and survive without issue, but that was another learning that sort of mirrors some of what the GSR tests faced when they dove with Patania II. They had a tether failure with their vehicle as well, so I’m looking forward to when we stop aiming to keep tethered, because, ultimately, that’s not part of the design of the vehicle.
SR: What sort of roles and people do you have on the Impossible Metals team?
JG: We really have a team that is built of a combination of industry expertise, as well as people that aren’t from the industry and bound by some of the same preconceived notions. I find that combination of existing know-how, “we’ve done it in the past”, combined with sort of appropriate levels of naivety but open-mindedness for creating and trying new things is a really good mesh for the team to develop these really novel solutions and develop them in a practical way that can actually work.
Really, we’ve designed the team with mechanical, electrical and software expertise, with also a real focus on controls and computer vision and AI related to the arms and the collection system as such a key part of our overall system.
SR: What strategy does Impossible Metals have in place to achieve its ambitious vision?
JG: Just stepping back, the most important things that we’ve ever done as humans are always ambitious things, and that’s some of what we’re really tapping into and proud of at Impossible Metals.
That being said, the way to achieve these ambitious things is really breaking them down into milestones and manageable individual steps. That’s really then the nature of how we’ve gone about testing and delivering this.
We have a phrase internally of “test early and test often”. A lot of times, you can sit there and think about a design and think things through, but until you’ve actually tested it, you’re going to miss the mark. We’d spend a lot of time figuring out that line between how much information and new knowledge can we get about the problem by thinking about it before just going and testing it and learning all those unknown unknowns.
SR: Is there anything else you think is worth mentioning?
JG: I think that the one key things is that the next version that we’re building – Eureka I had one arm, Eureka II has three arms – Eureka III will be our first production-size system. This will be the size of the system that we will actually be going out and doing mining operations with. It’s a 16-arm system and is that next step in our overall operations, which will we see as a more environmental approach but also a cost-comparable approach to the alternatives.
Sign up for our daily news round-up!
Give your business an edge with our leading industry insights.