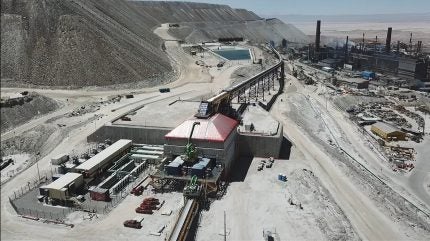
Automation and digitalisation have been hot topics in the mining industry for some time, with different companies further along in their digitalisation journey than others. It is well understood that deploying machines underground to work 24-7 can create operational efficiencies and improve safety – but there is another important benefit to be gained from underground automation: lowering project GHG emissions.
In EY’s 2024 annual survey of mining executives, environmental, social and governance (ESG), capital, licence to operate and climate change filled the top spots. When asked what ESG factors are facing the most scrutiny from investors in 2024, 46% said attaining net-zero emissions.
It is clear that reducing operational emissions is becoming a major focus for miners. As outlined in an OECD report, Mining and Green Growth in the EECCA Region, underground autonomous mining equipment has a key role to play in improving the sustainability of mines. For example, it highlights that automated ventilation systems at underground mining sites can save up to 40% of energy costs, in turn lowering operational emissions.
Another report, produced by academics in Canada and looking specifically at underground copper mining, is similarly positive. Its mine life cycle assessment finds that the reductions in CO₂ emissions from using automated equipment, and increasing efficiency and displacing diesel trucks, could decrease global warming potential by 17.9kg of CO₂ equivalent per tonne of ore.
This is significant given that global copper demand, driven by AI and the energy transition, is expected to increase by 29% by 2030, according to GlobalData.
Autonomous haulage systems move underground
Surface mining has been quicker to adopt automation than underground mining. This is because it is easier to install communications and GPS systems, which underpin automation, above ground than below.
Access the most comprehensive Company Profiles on the market, powered by GlobalData. Save hours of research. Gain competitive edge.

Your download email will arrive shortly
We are confident about the unique quality of our Company Profiles. However, we want you to make the most beneficial decision for your business, so we offer a free sample that you can download by submitting the below form
By GlobalData
However, investment in automation for underground mining is increasing and looks set to pick up pace, says Ben Moens, managing director at ENGIE Impact, a consultancy that works with companies to meet their sustainability goals.
“Underground mining is becoming more challenging as time goes on because much of the low-hanging fruit has mostly been done, so mines are getting deeper or more remote,” he says. “This will put greater emphasis on the automation of underground mining to ensure that mining can be done in an efficient, safe and sustainable way.”
Recent investments in an autonomous haulage system by Canadian gold producer Alamos Gold at its Young-Davidson mine in northern Ontario are illustrative of this trend.
As part of a lower mine expansion in 2020, the company installed a 600m electric conveyance and hoisting system to transport ore out of the mine. The system, which is digitally managed by a single hoist operator above ground, replaced six diesel haul trucks, reducing the mine’s overall fossil fuel requirements. It is also powered by the Ontario grid, which is majority supplied with low-carbon power.

As such, the system has halved the mine site’s GHG emissions intensity compared with 2020 (before the expansion), says Luc Guimond, chief operating officer at Alamos Gold. The conveyance system, compared with the diesel trucks, requires less maintenance, personnel and ventilation.
“The motivation for switching from diesel haul trucks to an electric conveyance system was to lower the mine’s overall cost profile and to achieve higher throughputs with the expansion but also reduce GHG emissions. They are really all intertwined,” he says. “We are now well set up for the long-term benefit, both from a cost perspective as well as a GHG emission intensity reduction perspective.”
The site is also transitioning to electric personnel carriers (it has three, with two more on order) and hybrid underground scoop trams.
A similar expansion is also under way at its Island Gold operations, also in Ontario. The current ramp system will be replaced with an electric-powered mine shaft, which will enable the mine to double production to 2,400 tonnes per day and displace around 12 diesel trucks.
Mine haul fleet electrification is one of the most effective and realistic ways to reduce CO₂ emissions in mining and help the industry reach its sustainability targets, says Jan Nyqvist, product manager for automation – underground mining at technology provider ABB Process Industries.
Nyqvist points to one of the world’s largest pieces of mining industry infrastructure, the 13km Takraf belt conveyor system installed at Codelco’s Chuquicamata underground mine project in northern Chile. The belt removes the equivalent of 120 large haul trucks for the transportation of copper ore, reducing CO₂ emissions by 70%, according to the mining operator. ABB employs 11 x 5MW gearless conveyor drives to move the belt, overcoming an altitude of 1.2km.

“Automation is a key contributor to reducing emissions,” says Nyqvist. “This is demonstrated by the automated, demand-based ventilation system we installed at Boliden’s mines in Sweden that returns annual energy savings of more than 50% compared to other systems – ventilating an entire mine can often cost half of the operating expenditure each year.”
In addition, working with Boliden and mining machine equipment provider Epiroc, with funding from Swedish innovation agency Vinnova, the three companies have developed, tested and demonstrated the world’s first fully battery-electric trolley truck system for underground mining. This has enabled the ABB Ability eMine trolley system to work underground after successful deployment in open-pit mines.
Integration challenges and new opportunities for interoperability
Integrating autonomous technology into a mine site can be challenging, however. Common issues include a lack of expertise within the company, the upfront capital cost and prioritising the investment and trust in the technology readiness.
“Adapting new automation technology requires personnel who are ready to change the way they are working, with established mining countries and those with high labour costs adapting quicker to automation,” explains Nyqvist.
In the future, new opportunities from digitalisation and automation will come from interoperability and the sharing of data across different autonomous equipment and between mines, says Moens.
“This can further drive efficiencies and carbon savings; with this data, and the leveraging of advancements in industrial computing as well as the use of algorithms, companies will have access to automatic identification and corrective action to solve a range of problems – from production and maintenance to safety,” he added.
Sustainability drivers to adopt this technology will certainly become more acute. Many miners already have net-zero ambitions and face mandatory emissions reporting. If they are to deliver the insatiable demand for new energy metals and minerals – between 2017 and 2022, demand for lithium tripled, demand for nickel rose by 40% and cobalt 70% – they will need to embrace the technology.
However, it is crucial for companies to not weigh up decarbonisation efforts against other initiatives – they must be thought of as a business imperative, alongside things like lowering costs or driving revenue, says Moens.
“In the mining industry, to ensure that companies stay competitive in a rapidly evolving market, as well as retaining the trust of stakeholders and customers, operating both efficiently and sustainably must be considered of utmost importance,” he concludes.
Sign up for our daily news round-up!
Give your business an edge with our leading industry insights.